There aren’t many topics that have been discussed more intensely than digitisation in the past twelve months. The pandemic has made us reconsider the way we live, work and think. Even things that would never have crossed our minds (for example, I would never have thought my six-year-old son would be learning to read and write via Teams) seem to have become normal. In this post, I’d like to look into the “new normal” of manufacturing projects – remote implementation.
ADAPTING TO CHANGE IS THE ONLY WAY FORWARD
During the first wave of the pandemic, in spring 2020, many manufacturing companies decided to put new projects on hold – simply because investing in them didn’t seem reasonable in such an unprecedented situation. In the past months, however, a completely different trend can be observed: leaders are even faster than before, and are taking major leaps in digital transformation. These “early adopters” have realized that waiting around isn’t going to do any good – because the world is probably not going to go back to the “old normal” any time soon (if ever).
There is no doubt manufacturing companies should (and are willing to) continue their digital transformation journey. But how can they successfully implement new technologies with all the restrictions that have been put in place (from social distancing to travel restrictions)? Is it possible to implement even complex tools such as an ERP, machine monitoring and supply chain management systems – without the project team being constantly on-site? These are the main questions that I’ll try to discuss in this article.
THE KEY TO A SUCCESSFUL REMOTE IMPLEMENTATION? PREPARATION
We have been involved in dozens of digitisation projects that were implemented with a minimum onsite presence of our team – so the covid crisis caught us quite prepared.
Everyone understands that working remotely is not just about teleconferences. Digital communication platforms are essential for all kinds of remote work; however, there are many other aspects that need to be considered when it comes to project implementation. You need to prepare a complex set of tools that can fully replace all the activities that are commonly performed on-site. Preparation is the key.
First of all, you should think about the following points:
1. Which project management tools are we going to use?
It doesn’t really matter if you decide to use an advanced project management system or if you’ll do with one or several spreadsheets. The important thing is for all the team members to know exactly how things are going to work and what is expected of them (and when).
2. How are we going to exchange information that is normally exchanged in the office, sometimes just “by the way” as the day goes?
3. How are we going to get the information that is normally gained by observing processes – typically on the shopfloor?
More on questions 2 and 3 follows.
COMMUNICATION PLATFORMS
When it comes to communication platforms, it’s not really about deciding whether to have a weekly team meeting on Webex, Zoom or Teams. You need to define the entire communication (or more precisely, collaboration) system for all the people/parties that are involved. “Back in the day,” when people met each other on a daily basis, information exchange happened naturally – as you met your coworker in the hall, at lunch, as you had a quick discussion in the office.
Now, it’s important to decide and define e.g.:
- where and how to share and pitch new ideas,
- where to keep track of open points, results etc.,
- when to use which communication channel (email, teleconferences/calls…)
- what are everyone’s responsibilities – who calls which meeting, who participates and what they are expected to share/present.
Otherwise someone will drop the project manager an email with a new idea, another person will discuss the progress with their team leader over the phone, yet another team member will try to solve an issue without recording it anywhere… – and it will be impossible for the team to stay on track.
EMPOWERMENT AND REMOTE COLLABORATION
When full-time on-site presence of key team members or external consultants is not possible during implementation, it is definitely challenging for the entire team – and it can pose a serious threat to the success of the project. Sometimes, the solution is to involve workers on the production floor and let them use (and build) their know-how. This way, a consultant can support them remotely and teach them e.g. to create a spaghetti diagram of a material flow. As the next step, the worker can work more independently on another value stream. It is essential to listen to production staff because it is on the shopfloor where the value is actually created. Finding a way to collect their ideas is a very important step – either directly (via agreed communication channels) or indirectly, via questionnaires, checklists etc.
There are a lot of implementation tasks that require observation. Normally, our consultants visit a customer’s site for a pre-implementation assessment (a plant tour). Since we had pre-covid experience with remote projects, we had developed a set of questions and checklists to go through before the project kick-off. With every remote implementation project, the list has become a little longer as new points have emerged. It has eventually grown into a complex questionnaire that serves as our virtual plant tour. We have learnt to carry out a very efficient online assessment that (together with essential multimedia – see below) can fully replace our onsite plant tours.
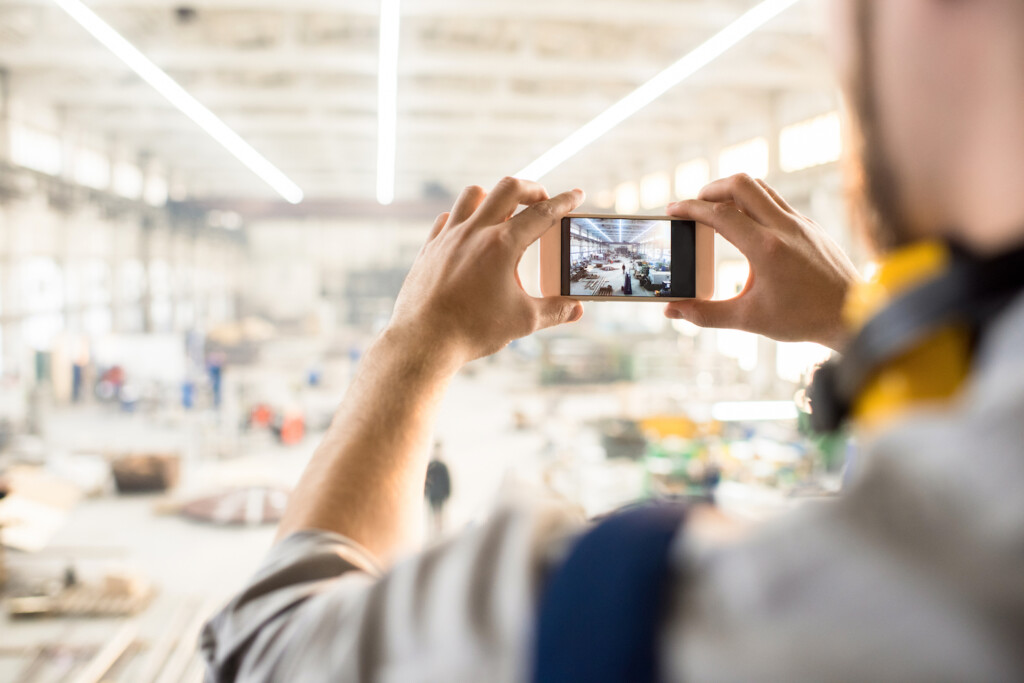
THE POWER OF MULTIMEDIA
As an old saying goes, a picture is worth a thousand words. Especially in manufacturing, where processes can be very complex, we find it more beneficial to ask for a picture or a video (e.g. of a material flow) rather than just verbal descriptions. Sometimes the worker taking the video wants to comment and share their ideas and opinions. Although this can be helpful in some situations, in others we prefer to get just the visual (recorded e.g. by a go-pro. The recording is then assessed and analyzed by a person with an unbiased perspective (which is very hard to achieve when talking about your daily bread).
Such a video can be used for other purposes, too – for employee training, for before/after comparisons, for measuring takt time, identifying wastes etc.
A quick snapshot or a short recorded sequence can also help solve many everyday problems during remote implementation (although not all of them, of course). Experienced consultants can use such multimedia to identify the issue and come up with a solution in the form of step-by-step instructions for the workers on-site (who successfully expand their skill set, i.e. become more empowered).
LESSONS LEARNED
What lessons have we learned from our recent remote implementation projects? That it is more and more meaningful for consulting businesses to get data analysts on board. Now that we cannot just hop on a plane and spend a week on a customer’s site, we need to rely on the data provided by the customer. And we need to be able to understand what is actually happening – not what the customer thinks is happening. Data analytics now constitutes a significant part of our work. The “new era” has also taught us to pay closer attention to training videos, tutorials, documentation as well as the user friendliness of the systems that are implemented.
If this was a real-time session (an online one, of course), I’d now ask you if you had any questions. This one might have popped into your head:
Of course this can happen. But as we emphasized at the beginning – preparation is the key to success. If a situation requires the onsite presence of a consultant, make sure everything that can be checked and prepared in advance is checked and prepared. Learn to be efficient. With a bit of luck, you can manage to implement a project just with one onsite visit (and a couple covid tests)!